Cerebras Unveils Wafer Scale Engine Two (WSE2): 2.6 Trillion Transistors, 100% Yield
by Dr. Ian Cutress on April 20, 2021 2:00 PM EST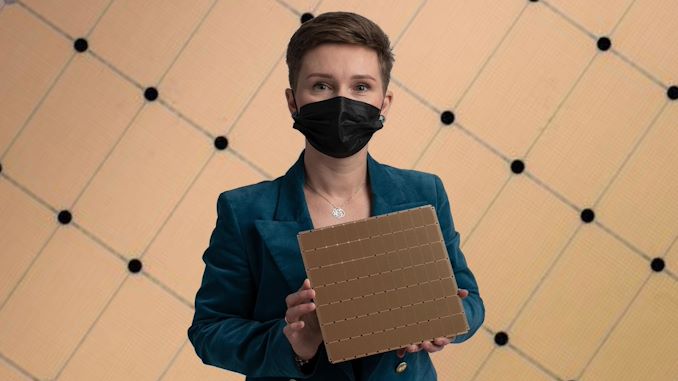
The last few years has seen a glut of processors enter the market with the sole purpose of accelerating artificial intelligence and machine learning workloads. Due to the different types of machine learning algorithms possible, these processors are often focused on a few key areas, but one thing limits them all – how big you can make the processor. Two years ago Cerebras unveiled a revolution in silicon design: a processor as big as your head, using as much area on a 12-inch wafer as a rectangular design would allow, built on 16nm, focused on both AI as well as HPC workloads. Today the company is launching its second generation product, built on TSMC 7nm, with more than double the cores and more than double of everything.
Second Generation Wafer Scale Engine
The new processor from Cerebras builds on the first by moving to TSMC’s N7 process. This allows the logic to scale down, as well as to some extent the SRAMs, and now the new chip has 850,000 AI cores on board. Basically almost everything about the new chip is over 2x:
Cerebras Wafer Scale | |||
AnandTech | Wafer Scale Engine Gen1 |
Wafer Scale Engine Gen2 |
Increase |
AI Cores | 400,000 | 850,000 | 2.13x |
Manufacturing | TSMC 16nm | TSMC 7nm | - |
Launch Date | August 2019 | Q3 2021 | - |
Die Size | 46225 mm2 | 46225 mm2 | - |
Transistors | 1200 billion | 2600 billion | 2.17x |
(Density) | 25.96 mTr/mm2 | 56.246 mTr/mm2 | 2.17x |
On-board SRAM | 18 GB | 40 GB | 2.22x |
Memory Bandwidth | 9 PB/s | 20 PB/s | 2.22x |
Fabric Bandwidth | 100 Pb/s | 220 Pb/s | 2.22x |
Cost | $2 million+ | arm+leg | ‽ |
As with the original processor, known as the Wafer Scale Engine (WSE-1), the new WSE-2 features hundreds of thousands of AI cores across a massive 46225 mm2 of silicon. In that space, Cerebras has enabled 2.6 trillion transistors for 850,000 cores - by comparison, the second biggest AI CPU on the market is ~826 mm2, with 0.054 trillion transistors. Cerebras also cites 1000x more onboard memory, with 40 GB of SRAM, compared to 40 MB on the Ampere A100.
Me with Wafer Scale Gen1 - looks the same, but with less than half the cores.
The cores are connected with a 2D Mesh with FMAC datapaths. Cerebras achieves 100% yield by designing a system in which any manufacturing defect can be bypassed – initially Cerebras had 1.5% extra cores to allow for defects, but we’ve since been told this was way too much as TSMC's process is so mature. Cerebras’ goal with WSE is to provide a single platform, designed through innovative patents, that allowed for bigger processors useful in AI calculations but has also been extended into a wider array of HPC workloads.
Building on First Gen WSE
A key to the design is the custom graph compiler, that takes pyTorch or TensorFlow and maps each layer to a physical part of the chip, allowing for asynchronous compute as the data flows through. Having such a large processor means the data never has to go off-die and wait in memory, wasting power, and can continually be moved onto the next stage of the calculation in a pipelined fashion. The compiler and processor are also designed with sparsity in mind, allowing high utilization regardless of batch size, or can enable parameter search algorithms to run simultaneously.
For Cerebras’ first generation WSE is sold as a complete system called CS-1, and the company has several dozen customers with deployed systems up and running, including a number of research laboratories, pharmaceutical companies, biotechnology research, military, and the oil and gas industries. Lawrence Livermore has a CS-1 paired to its 23 PFLOP ‘Lassen’ Supercomputer. Pittsburgh Supercomputer Center purchased two systems with a $5m grant, and these systems are attached to their Neocortex supercomputer, allowing for simultaneous AI and enhanced compute.
Products and Partnerships
Cerebras sells complete CS-1 systems today as a 15U box that contains one WSE-1 along with 12x100 GbE, twelve 4 kW power supplies (6 redundant, peak power about 23 kW), and deployments at some institutions are paired with HPE’s SuperDome Flex. The new CS-2 system shares this same configuration, albeit with more than double the cores and double the on-board memory, but still within the same power. Compared to other platforms, these processors are arranged vertically inside the 15U design in order to enable ease of access as well as built-in liquid cooling across such a large processor. It should also be noted that those front doors are machined from a single piece of aluminium.
The uniqueness of Cerebras’ design is being able to go beyond the physical manufacturing limits normally presented in manufacturing, known as the reticle limit. Processors are designed with this limit as the maximum size of a chip, as connecting two areas with a cross-reticle connection is difficult. This is part of the secret sauce that Cerebras brings to the table, and the company remains the only one offering a processor on this scale – the same patents that Cerebras developed and were awarded to build these large chips are still in play here, and the second gen WSE will be built into CS-2 systems with a similar design to CS-1 in terms of connectivity and visuals.
The same compiler and software packages with updates enable any customer that has been trialling AI workloads with the first system to use the second at the point at which they deploy one. Cerebras has been working on higher-level implementations to enable customers with standardized TensorFlow and PyTorch models very quick assimilation of their existing GPU code by adding three lines of code and using Cerebras’ graph compiler. The compiler then divides the whole 850,000 cores into segments of each layer that allow for data flow in a pipelined fashion without stalls. The silicon can also be used for multiple networks simultaneously for parameter search.
Cerebras states that with having such a large single chip solution means that the barrier to distributed training methods across 100s of AI chips is now so much further away that this excess complication is not needed in most scenarios – to that, we’re seeing CS-1 deployments of single systems attached to supercomputers. However, Cerebras is keen to point out that two CS-2 systems will deliver 1.7 million AI cores in a standard 42U rack, or three systems for 2.55 million in a larger 46U rack (assuming there’s sufficient power for all at once!), replacing a dozen racks of alternative compute hardware. At Hot Chips 2020, Chief Hardware Architect Sean Lie stated that one of Cerebras' key benefits to customers was the ability to enable workload simplification that previously required racks of GPU/TPU but instead can run on a single WSE in a computationally relevant fashion.
As a company, Cerebras has ~300 staff across Toronto, San Diego, Tokyo, and San Francisco. They have dozens of customers already with CS-1 deployed and a number more already trialling CS-2 remotely as they bring up the commercial systems. Beyond AI, Cerebras is getting a lot of interest from typical commercial high performance compute markets, such as oil-and-gas and genomics, due to the flexibility of the chip is enabling fluid dynamics and other compute simulations. Deployments of CS-2 will occur later this year in Q3, and the price has risen from ~$2-3 million to ‘several’ million.
With Godzilla for a size reference
Related Reading
- Cerebras Wafer Scale Engine News: DoE Supercomputer Gets 400,000 AI Cores
- 342 Transistors for Every Person In the World: Cerebras 2nd Gen Wafer Scale Engine Teased
- Cerebras’ Wafer Scale Engine Scores a Sale: $5m Buys Two for PSC
- Hot Chips 2020 Live Blog: Cerebras WSE Programming (3:00pm PT)
- Hot Chips 2019 Live Blog: Cerebras' 1.2 Trillion Transistor Deep Learning Processor
136 Comments
View All Comments
bernstein - Tuesday, April 20, 2021 - link
call me dumb, but why not create a round cpu, filling the entire wafer?! or half moon shaped for two per wafer? the quadratic design seems rather wasteful...qap - Tuesday, April 20, 2021 - link
Because you need to make it using tiles and there are only so many regular tiles that can fill the surface without overlap or gaps. And rectangle is the most practical. I heard some arguments for hexagons but I don't see that happening.III-V - Tuesday, April 20, 2021 - link
Because this is easier to make. Ultimately the wafer cost is rather trivial, if these things are selling for $2M a pop.FreckledTrout - Tuesday, April 20, 2021 - link
Go to google images and search for "Die shot". A core is made up of a lot of little logic and cache areas. When you start combing those together to then etch the entire die its much easier to pack them if they are square/rectangular. Unfortunately you can easily make square wafers either. So there is some waste but it gets recycled.Zizy - Tuesday, April 20, 2021 - link
It needs to be pointed out that the chip costs about 5m while each processed wafer is about 10k. Even if you halve price of the chip and double it of the silicon, we are still looking at silicon costs at 1% of the chip price. Insignificant.Second, this waste isn't so large - from the calculation of the wafer area and this huge chip size given in this article, about 2/3 is useful and 1/3 of the wafer gets wasted. Not too bad.
Finally, at once you illuminate 23x33mm - reticle limit. The chip is made by tiling such structures over the whole wafer - whereas say A100 has each individual chip just under the reticle limit. Stuff that is partially beyond the wafer is most likely dead anyway, so at most there would be quite few extra reticle-sized features present. But this is maybe 5%. Probably discarded for simplicity in both dicing (no need to do anything fancy) as well as communication (other cores have 2 neighbors at least, some of these may not).
Ian Cutress - Tuesday, April 20, 2021 - link
A full CS-1 system costs $2-2.5m.HammerStrike - Tuesday, April 20, 2021 - link
The benefit of using the whole water would be additional logic on each completed chip, not cost saving from not wasting potential die area.Whether or not that’s feasible is a different story.
EthiaW - Tuesday, April 20, 2021 - link
At low volume the majority of cost comes from one-time expenditure such as EDA software and lithography masks. For 7nm this will cost tens of millions, or more than 1m per unit actually.brucethemoose - Thursday, April 22, 2021 - link
I think it would make the interconnect (just look at that partitioning illustration), and the core redundancy scheme, more complicated.In other words, I bet TSMC could do it, but reworking the design to work in such a way would be difficult.
bryanlarsen - Thursday, April 22, 2021 - link
TSMC's reticles are rectangular so it has to be made of the rectangles you see in the pictures. However, I'm not sure why they don't have additional rectangles in the middle of the sides. Maybe the rectangles are so big that none would fit.